Unveiling the Importance of Factory Connection: A Comprehensive Guide
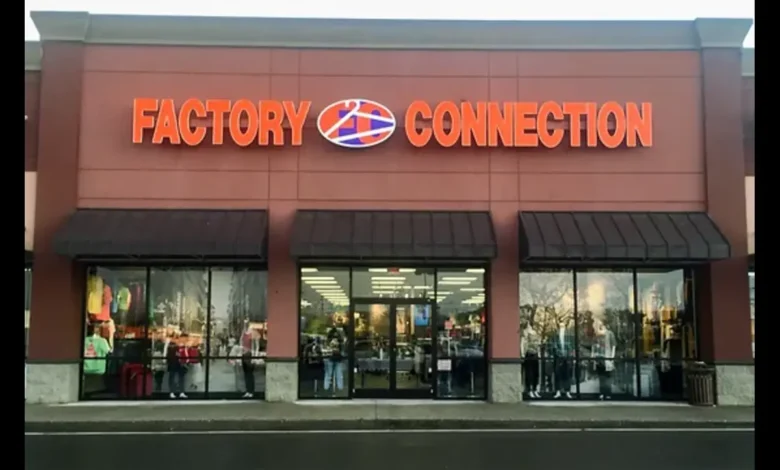
Introduction:
In today’s rapidly evolving industrial landscape, establishing a seamless connection between factories is paramount for sustainable growth and operational efficiency. This article delves into the significance of factory connection, its implications across various industries, and the strategies to optimize this vital aspect of modern manufacturing.
Understanding Factory Connection: Factory connection refers to the integration of multiple manufacturing units, often geographically dispersed, into a cohesive network. This network facilitates streamlined communication, data sharing, and resource allocation among different production facilities. By establishing robust connections between factories, organizations can enhance production capacity, minimize costs, and respond swiftly to market demands.
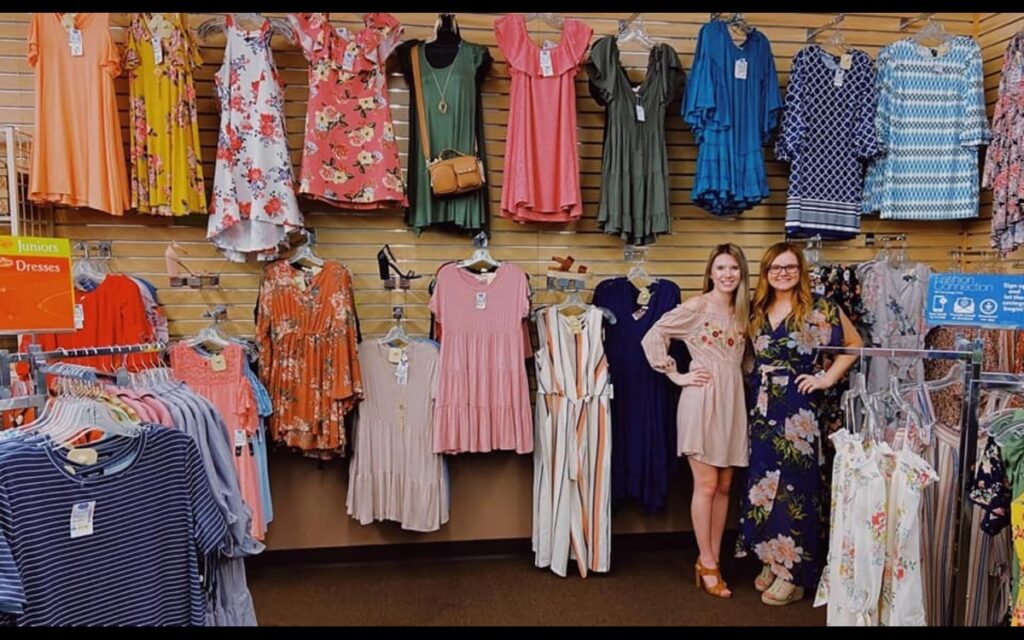
Importance of Factory Connection:
- Enhanced Collaboration: Interconnecting factories enables seamless collaboration between different teams and departments. Whether it’s sharing design blueprints, production schedules, or quality control standards, a connected network fosters collaboration and accelerates decision-making processes.
- Optimized Resource Utilization: Through factory connection, organizations can optimize the utilization of resources such as raw materials, equipment, and workforce. By centralizing inventory management and production planning, companies can minimize wastage and maximize operational efficiency.
- Improved Flexibility and Agility: In today’s dynamic market conditions, adaptability is key to sustaining competitiveness. Factory connection empowers organizations to adapt quickly to changing customer preferences, market trends, and unforeseen disruptions by reallocating resources and adjusting production processes across interconnected facilities.
- Real-time Monitoring and Control: Leveraging advanced technologies such as Internet of Things (IoT) sensors and data analytics, interconnected factories enable real-time monitoring of production processes and equipment performance. This proactive approach allows organizations to identify inefficiencies, address bottlenecks, and ensure consistent product quality across all manufacturing sites.
- Global Reach and Scalability: For multinational corporations, factory connection offers the ability to scale operations globally while maintaining centralized control and coordination. By establishing connections between factories located in different regions, companies can tap into new markets, leverage local expertise, and achieve economies of scale.
Optimizing Factory Connection:
- Invest in Connectivity Infrastructure: To establish robust factory connections, invest in reliable networking infrastructure such as high-speed internet connectivity, VPNs (Virtual Private Networks), and secure communication protocols. Additionally, consider implementing cloud-based collaboration platforms to facilitate seamless data sharing and communication between geographically dispersed teams.
- Adopt Industry 4.0 Technologies: Embrace Industry 4.0 technologies such as IoT, big data analytics, and artificial intelligence to enhance connectivity, automation, and intelligence across manufacturing operations. By integrating smart sensors and connected devices into production equipment, organizations can gather real-time data insights to optimize processes and improve decision-making.
- Standardize Processes and Protocols: Standardizing processes and protocols across interconnected factories is essential to ensure consistency, efficiency, and compliance with regulatory standards. Establish clear communication channels, standardized workflows, and quality control measures to minimize discrepancies and ensure uniformity in product quality across all manufacturing sites.
- Train and Empower Workforce: A connected factory ecosystem requires a skilled workforce capable of leveraging digital tools and technologies effectively. Invest in training programs to upskill employees and empower them to adapt to new technologies and workflows. Encourage a culture of continuous learning and innovation to drive organizational growth and competitiveness.
- Monitor and Evaluate Performance: Regularly monitor and evaluate the performance of interconnected factories using key performance indicators (KPIs) such as production output, resource utilization, and quality metrics. Identify areas for improvement, implement corrective actions, and iterate on strategies to optimize factory connections continuously.
FAQs (Frequently Asked Questions):
Q1. What are the common challenges associated with establishing factory connections? A1. Common challenges include compatibility issues between disparate systems, cybersecurity risks, data privacy concerns, and resistance to change among employees.
Q2. How can small and medium-sized enterprises (SMEs) benefit from factory connection? A2. SMEs can benefit from factory connection by gaining access to shared resources, expanding market reach, improving operational efficiency, and competing more effectively with larger corporations.
Q3. What role does data analytics play in optimizing factory connections? A3. Data analytics enables organizations to gather insights from vast amounts of data generated by interconnected factories, leading to informed decision-making, predictive maintenance, and continuous process improvement.
Conclusion:
Factory connection is not merely a technological advancement but a strategic imperative for modern manufacturing organizations. By embracing connectivity, collaboration, and innovation, businesses can unlock new levels of efficiency, agility, and competitiveness in today’s interconnected world. As Industry 4.0 continues to reshape the manufacturing landscape, the importance of establishing robust factory connections will only intensify, driving sustainable growth and resilience across industries.